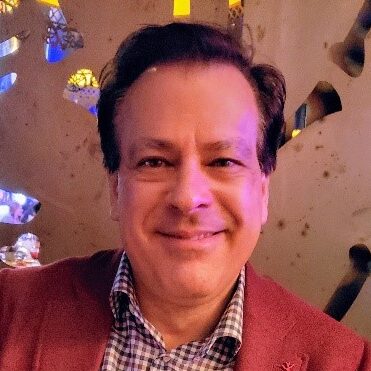
Murray Pearson 
Director,Technology Development, High Pressure Metallurgy
Hatch
Murray has 30+ years of experience in engineering and design of specialty chemical and metallurgical process plants, including a diverse background in mechanical, piping, instrumentation, estimating, procurement, and project engineering. His project assignments include feasibility studies and detailed design of autoclave facilities & related processes for the oxidation & extraction of non-ferrous metals. Between 2003 and 2006, Murray oversaw the engineering and design of novel demonstration plants for chloride assisted oxidative leaching of nickel and copper sulphides and commercial processing of Pentlandite. From 2008 to 2012, Murray supervised the mechanical design of the pressure oxidation facility for the Pueblo Viejo Project, a 24 000 t/d refractory gold plant located in the Dominican Republic. He is presently the project manager for JSC Polymetal's Phase 4 POX Hub Expansion Project. Murray graduated with a Bachelor of Engineering from the University of Saskatchewan, and an MBA from Smith School of Business.
Treatment of Double-Refractory Sulphide Concentrates in Russia
In May 2020, Hatch released the world’s largest, custom designed, high-temperature autoclave for installation at Polymetal JSC's Phase 4 POX Hub Expansion Project located near Amursk, Khabarovsk. With an operating temperature of 240°C and operating pressure of 52 bar(g), the Amursk autoclave is the heart of a new POX circuit that will process double-refractory (high organic carbon) sulphide gold concentrates. The design pressure is 50% higher than that of other POX autoclaves currently in operation, and the process volume approximately 2X that of the largest autoclaves built previously by Hatch.
Polymetal engaged Hatch to provide engineering and procurement support services for the POX facility, utilities, off-gas treatment, heat recovery, and slurry conditioning areas. Hatch also supplied the custom-designed process equipment for the facility, including flash vessels, vent gas cyclone, refractory linings, pressure letdown valves, vent gas condensers, dip pipes, and oxygen spargers. Among the unique features of this facility: the ability to treat concentrates with high arsenic and high organic carbon with > 90% gold recovery, highly efficient heat recovery, and state-of-the-art vent gas cleaning.